Aluminum thermal analysis has made great progress since the 1970’s when the first systems were introduced. Today we can not only look at the undercooling of the liquidus to measure inoculation, and the degree of modification of the eutectic, we can actually measure the energy produced by the various phases precipitating out including the copper and magnesium phases as well as the iron (beta crystal) phases.
Aluminum Thermal Analysis uses area integration to measure the amount of heat of fusion for individual phases as a ratio against the overall energy of fusion of the sample. While the temperature curve shows large arrests happening, the rate of cooling curve (1/1st derivative) shows the energy of much smaller events. MeltLab uses 2nd, 3rd, and 4th derivatives to pinpoint the start and stop of each phase. Sampling is done with a small steel cup from the molten bath that has been coated with Boron Nitride using a Pechiney style stand. The analysis is fully automated by a PC connected through a super accurate analog to digital converter to the shielded thermocouple.
Choose your type of Aluminum to view the Cooling Rate and Curves:
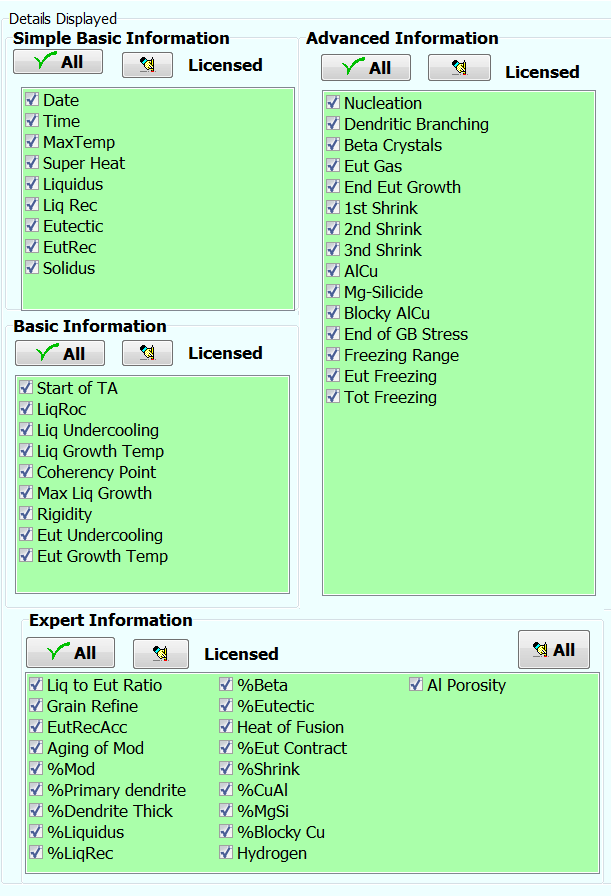
This system can be used to quantify the conditions of molten metal before casting so that the various phases can be adjusted through additions, inoculation, and modification. Results can be easily displayed in Fahrenheit or Celsius by clicking on the C/F button in the lower right corner. Integrated precision at the 99% confidence level is around 0.03% of total energy. At the 95% confidence level, precision is about 0.01% on the foundry floor.
Click HERE to return to Our Software